
left hand side is all the Opto-isolators for the input side to the TB6560 chips. Last picture if of the board, sorry fuzzy but all taken with camera phone. The green ground wire goes off to the Clamp which is clamped again to the Plasma frame and back to the negative terminal on the plasma cutter:. Next is the copper ground connected to the nozzle, the idea of this is to stop the sputtering, if possible and provide a sort of pilot earth. Inside shot of the box, again note the grounding stubs bottom left of the door area, three green wires go up to the screens on the output cables, also there is connection from the door earth stud to the main box earth sud and the mains is also filtered:. OK some pictures, first one is the grounding connection to the back of the plasma unit, ,įrom here it goes to to the underside of the main frame and the disposable frame the metal being cut sits on:-įrom here a grounding strap goes up to the control box, bottom left of the picture:.

So not a case of one part open but both outputs of the chip just very low output. Have toi use AC on the meter during stepping as it switched pos to neg, neg to pos etc. On a duff drive either X or Z axis I only get around 6 Volts AC. On the Y axis that still works when I move a stepper motor I get 25 Volts AC across the AP and AM connections and the same across the BP and BM windings. A few pictures taken these are below and I also put back in my duff control board before I repair it. The power supply is a Lambda power supply as mentioned. Run the plasma up with out covers and the HF unit is not running all the time, just on start-up and when the nozzle goes over a hole when you can hear the sort of juddering when it takes out the control gear. This will help it make a stronger conductive electrical charge.OK just managed to get 20 minutes in the garage. Use an emery cloth to wipe off the cutting tip so that it has a shine to it. Like a battery cable, this will cut down on the amount of charge it can build up. Clean TipĪfter some use, the tip can build up a lot of dust. Make sure you take the time to clean the surface of any dust, oil, rust, or other contaminates that can hamper the electrical current. Since the plasma cutter works through making a conductive connection with the piece that it is cutting, you will see problems when the metal surface is dirty. Keep a supply of new cutting tips on hand so you can quickly change them. If it gets any larger the conductivity of the electric charge will not work as efficiently. As the cutter is working, it will burn back the tips so that the cutting hole is misshapen. One inherent problem with the plasma cutter is that it can burn through tips very quickly. When this happens you should stop cutting and wipe off the end of the tip to clean it of any dust or slag.

This slag, or metal dust, can cause the electrical current to discharge and not make a good connection. Clogged Cutting TipĪs the plasma cutter is working, there is a tendency to collect dirt particles and metal slag. Make sure that you can keep this level maintained. The cubic feet per minute rating on the air compressor should be set at the specified amount that is determined in the owner's manual. Keep Air Pressure UpĪs the cutter is working, the built in air compressor does the work of blowing away the cut material and debris.
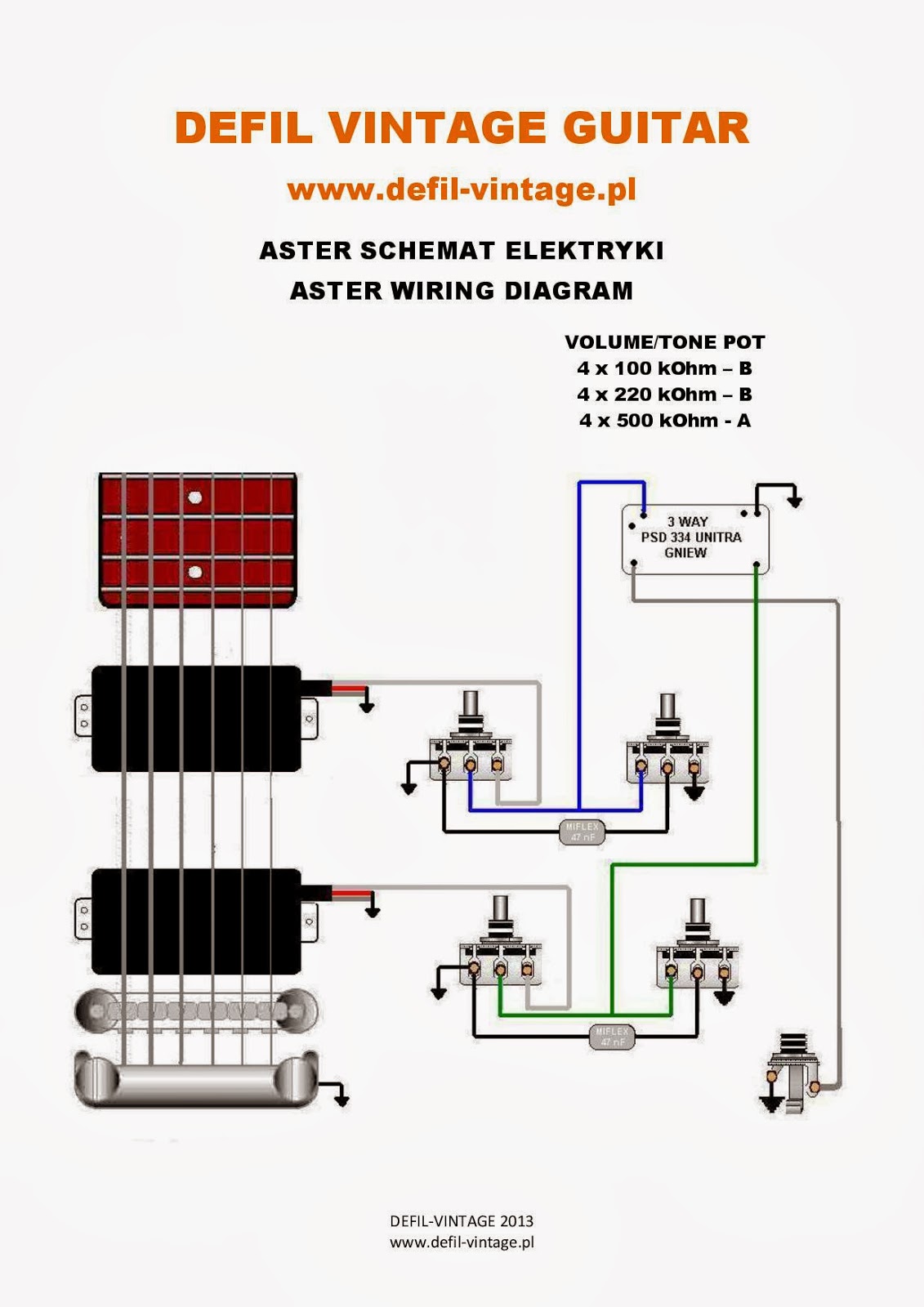
Make sure the connections on the ground clamp are good. This completes the circuit so that the cutter can create the charge it needs to melt away the metal. There is a grounding clamp that must be connected to the workpiece, near where you are making your cut. The plasma cutter must also be grounded through the workpiece. The plasma cutter must be grounded correctly in order for the electrical arc to work. The outlet may have the third prong available, but it isn't set up as a true grounded outlet. One of the problems people run into with plasma cutters is that they do not plug them into 3 pronged, grounded outlets.
